Packaging Machines and Other Advancements Within the Food and Beverage Industry
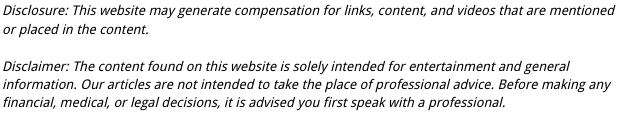

When you’re in the food and beverage industry, you realize the importance of having safe and economical product packaging. Furthermore, you’re also likely concerned with making an environmental and social difference by reducing waste and engaging in other proactive practices. You may be aware that 52% of the global population makes purchase decisions based on these and other values, such as having access to consistently high-quality products.
Reducing Waste by Packaging Products in Plastic
According to packaging experts, food waste can be reduced with plastic packaging. These experts estimate that this can be as much as 1.7 pounds of food for every pound of plastic packaging. When plastic, rather than other types of materials are used to contain beverages, this can make a difference with container waste and preserve food quality. Just two pounds of plastic, for example, can contain about ten gallons of beverages, which includes juice, soda, water, and other fluid-containing bottles.
When compared with other types of containers, such as aluminum, steel, and glass, plastic can contain more fluids and produce less waste.
- Aluminum beverage containers: Three pounds is needed to contain about ten gallons
- Steel beverage containers: Eight pounds is needed to contain about ten gallons
- Glass beverage containers: 40 pounds of glass is needed to contain about ten gallons
Maintaining Food Health and Safety Standards
On an annual basis, there are approximately 48 million people that become ill from food-borne diseases. Approximately 128,000 of these individual will require hospitalization, and 3,000 will die as a result of coming into contact with contaminated food.
In many instances, food-borne illnesses can be eliminated with proper storage methods. Since cold temperatures are able to prevent harmful bacteria from developing and multiplying, refrigerators need to be set no higher than 40 degrees Fahrenheit. When food is stored in freezers, the temperature should be set at zero degrees Fahrenheit.
In addition to a variety of food-borne illnesses and contaminants, foreign objects, such as metals, may be present in some products. Given this, the use of X-ray machines for food inspection is strongly recommended. These machines are able to identify three types of metallic contaminates: ferrous, non-ferrous, and stainless steel. it is important to note the superiority of X-ray inspections, as a typical food metal detector is unable to sense these substances to the same degree.
When a standard metal detector is applied to a wet or conductive food product, for instance, 2.5 to 3.5 millimeters of stainless steel particles can be detected. However, when an X-ray food inspection machine is employed, it is able to detect metallic particles of 1.5 millimeters or even smaller. In addition to improving food safety, this can also preserve a brand’s reputation for providing safe, high-quality products.
Packaging machines can make a significant impact on the maintenance of health and safety standards as well as food quality. When food is vacuum-sealed, for example, it will last about three to five times longer than when stored in containers or plastic bags. This also reduces food waste, which is important for business as well as the customer experience.
Learn More About Other Industry Advancements
Given technological advancements in the food and beverage industry, from more economical and environmentally-friendly packaging to food safety inspection devices, you may be interested in learning more about the food packaging machines that are currently available. In addition to packaging machines, you may also be interested in learning more about best-practices updates within this industry. Since you want to provide your customers with the highest-quality products, enhance their experience, and build brand loyalty, it makes sense to consult with a packaging expert on these and other relevant industry issues.